În ultimii 100 de ani, uzinele care produc mașini au arătat în mare parte la fel: un furnicar de oameni și conveiere (sau benzi transportoare, în limbaj popular) care lucrează împreună pentru a oferi lumii întregi un produs finit devenit indispensabil. Este vorba despre automobil.
Cu timpul, mașinile au devenit tot mai complexe. La fel și producția. În consecință, constructorii de automobile au fost nevoiți să se adapteze noilor condiții și să creeze un proces de asamblare cât mai eficient și sustenabil.
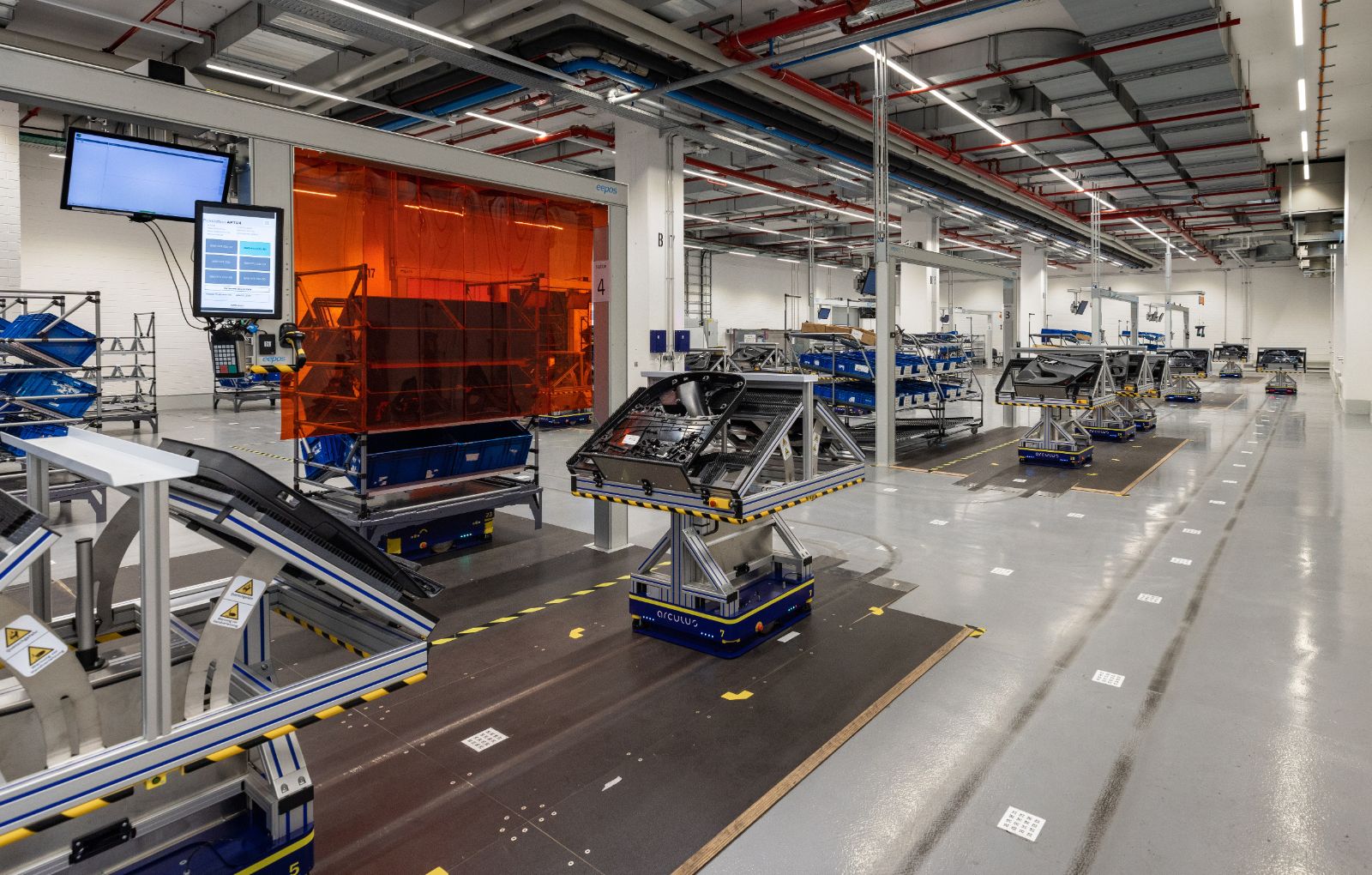
Audi, prin „Automotive Initiative 2025”, este una dintre mărcile care caută constant soluții inteligente pentru producția viitorului.
Majoritatea ideilor vin din Laboratorul de Producție, înființat în 2012. Pe scurt, un spațiu futurist, în care o mână de minți luminate testează diverse sisteme inteligente de asistență care au rolul de a conserva resursele și de a îmbunătăți siguranța și ergonomia la locul de muncă.
Desigur, constructorul german de automobile primește ajutor și din afară, având o colaborare strânsă cu Universitatea Tehnică din Munchen și cu Institutul pentru Inginerie Industrială Fraunhofer.
Odată identificate, aceste tehnologii inovatoare sunt integrate în diverse secvențe ale producției.

ASAMBLAREA MODULARĂ, O INOVAȚIE AUDI
Într-un proces de producție tot mai complex, benzile rulante pe care le-am menționat mai sus încep să își arate limitele. Soluția găsită de Audi este așa numita asamblare modulară, un proces care nu se mai bazează pe un conveier sau pe un ritm uniform de lucru.
În locul unei benzi transportoare fizice, avem stații independente și dinamice, secvențe variabile și timpi de procesare dependenți de fiecare versiune în parte. Sună destul de complicat, dar Audi compară acest proces cu o bandă transportoare virtuală.
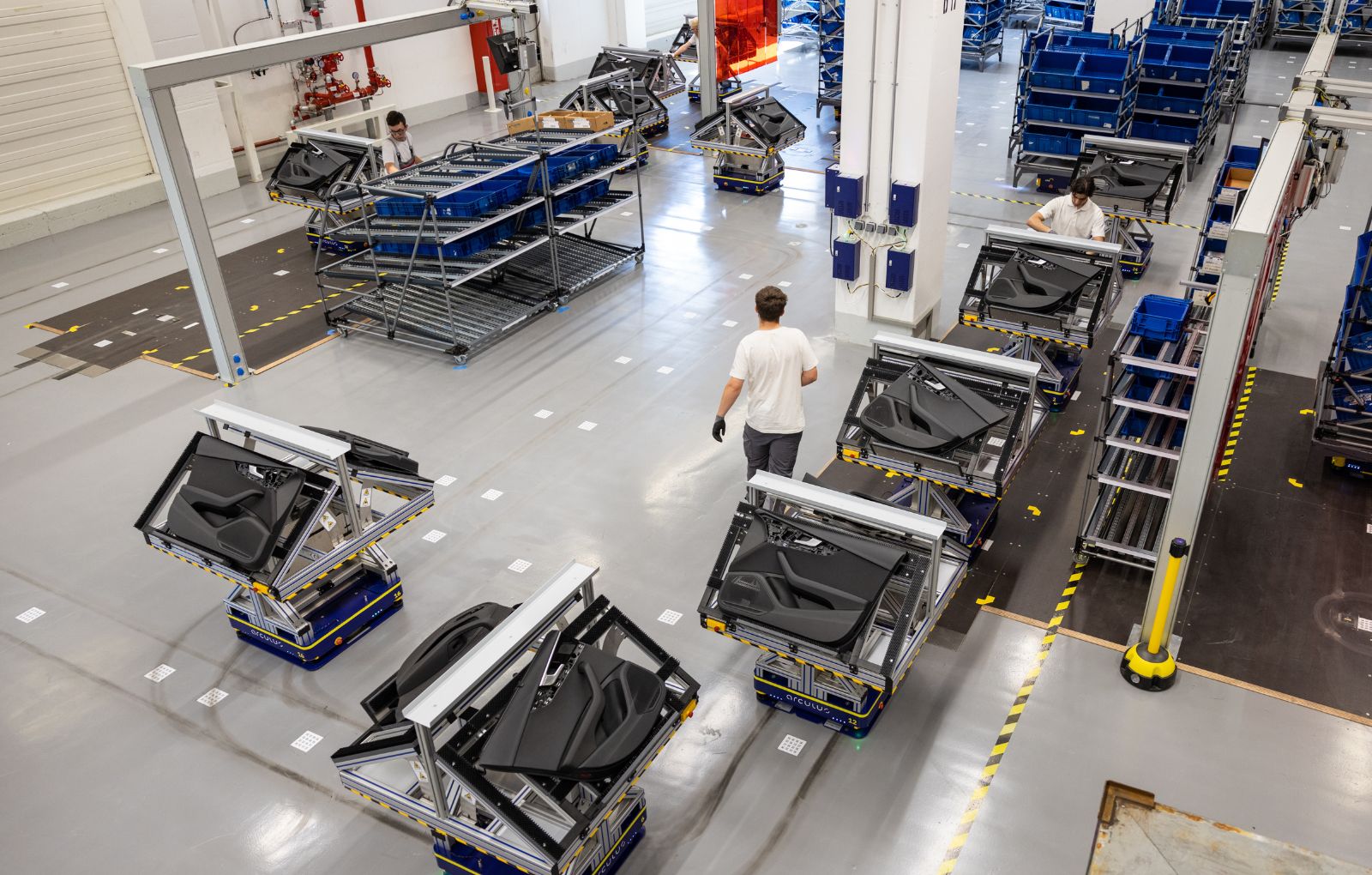
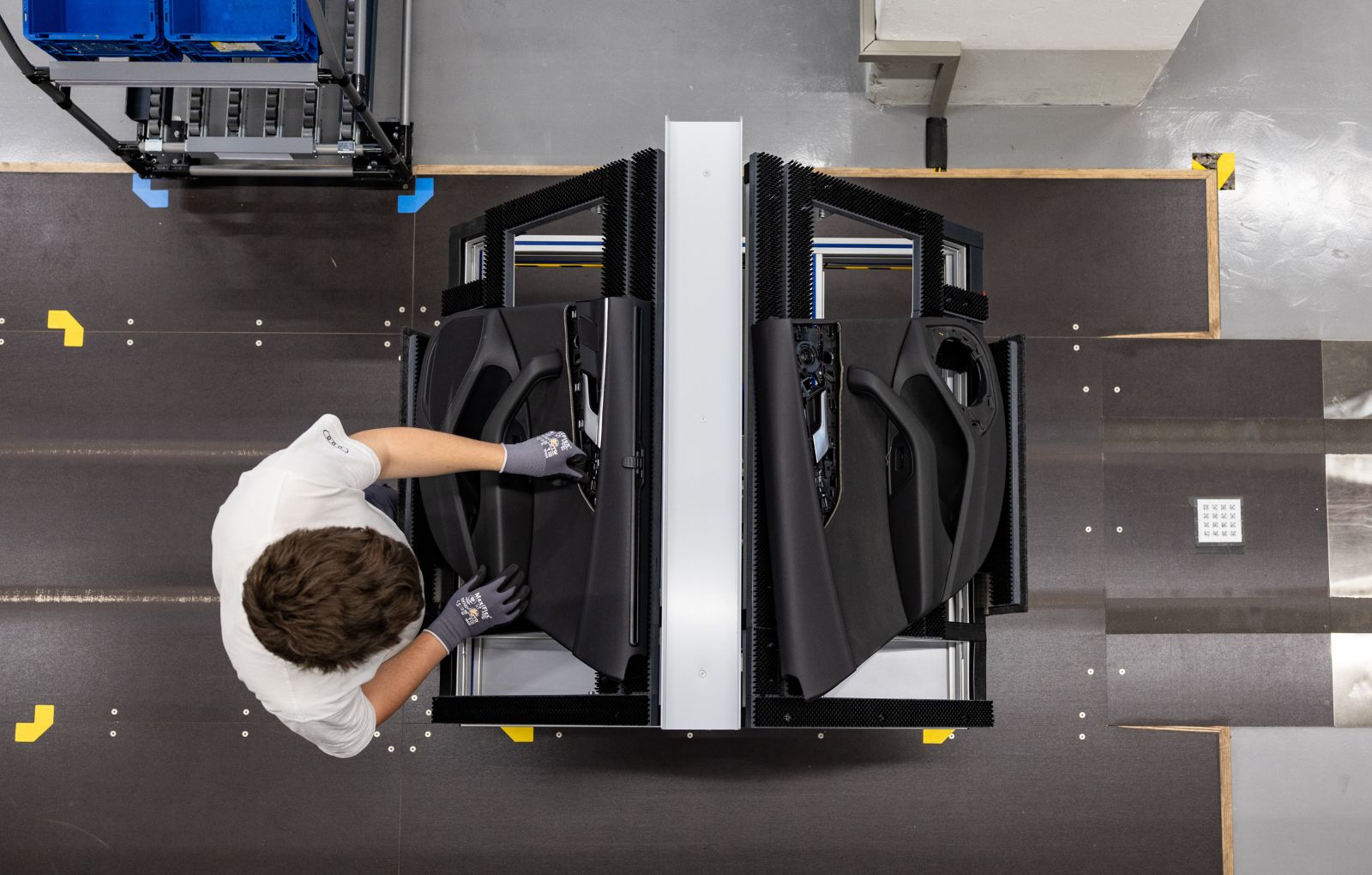
„Asamblarea modulară este unul dintre răspunsurile noastre la viitoarele cerințe de producție. Folosim digitalizarea în beneficiul angajaților noștri, realizând în același timp o asamblare flexibilă și eficientă,” susține Gerd Walker, manager de proiect în cadrul Laboratorului de Producție și membru în consiliul director pentru Producție și Logistică.
O premieră în industria auto, Audi implementează acest concept în cadrul secției de pre-asamblare a panoului interior al portierei, la uzina din Ingolstadt. Dacă va da roade, asamblarea modulară va fi utilizată, la scară largă, în întregul proces de pre-asamblare începând cu anul 2025.
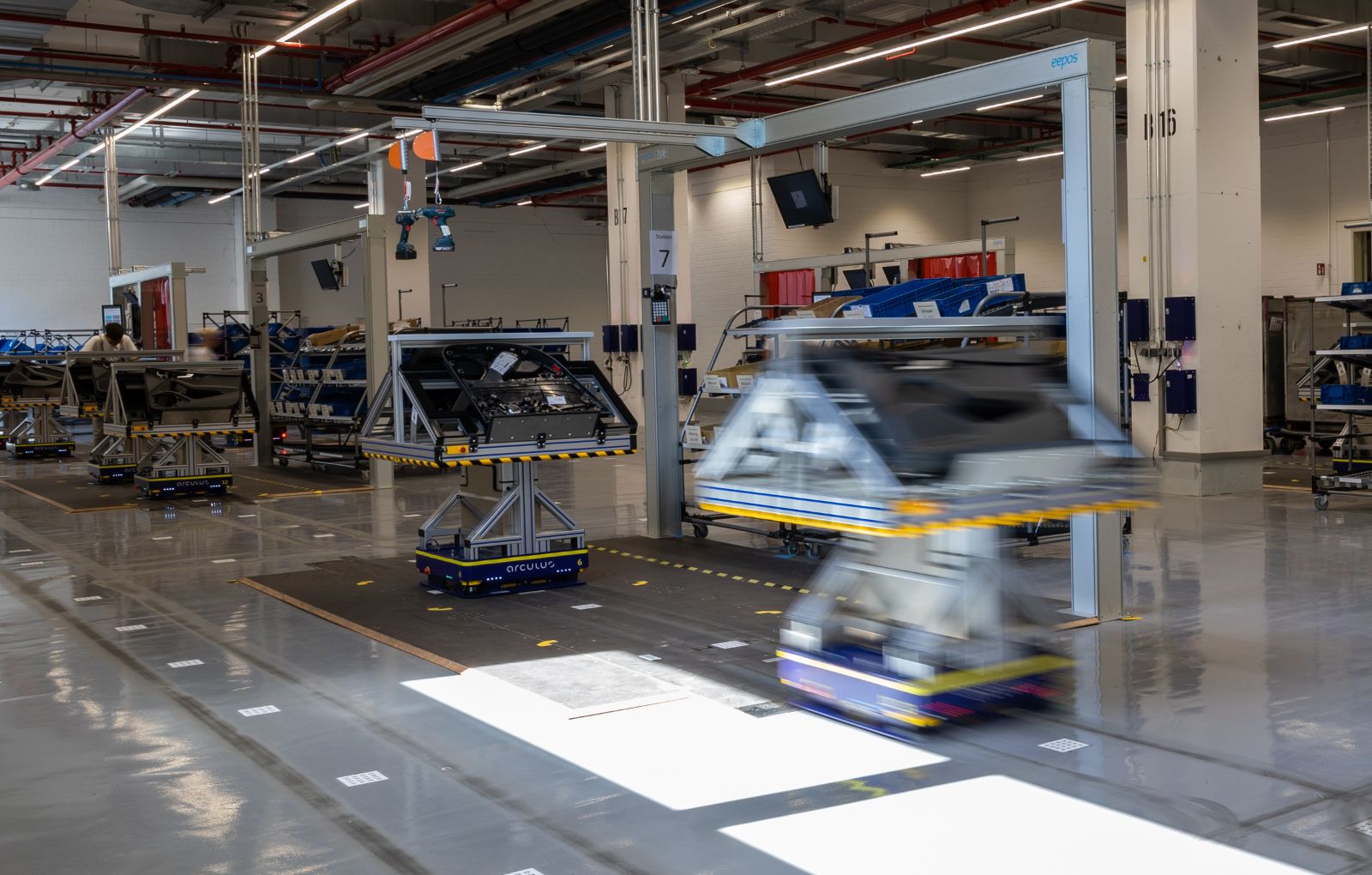
În cadrul proiectului pilot, secvența de lucru nu mai este uniformă. Spre exemplu, vehicule ghidate automat de un computer central (AGV) aduc panourile portierelor direct la bancul de lucru, iar un singur lucrător instalează componentele.
Chiar și instalarea unui parasolar pentru ușile spate (dotare opțională) poate fi realizată de un singur om. La un sistem cu benzi transportoare, acest proces ar fi implicat două sau trei persoane, susțin reprezentanții Audi.
Nu în ultimul rând, dacă lucrătorul de la un anumit banc este prea ocupat, AGV-urile transportă componenta respectivă la bancul de lucru cu cel mai mic timp de așteptare.
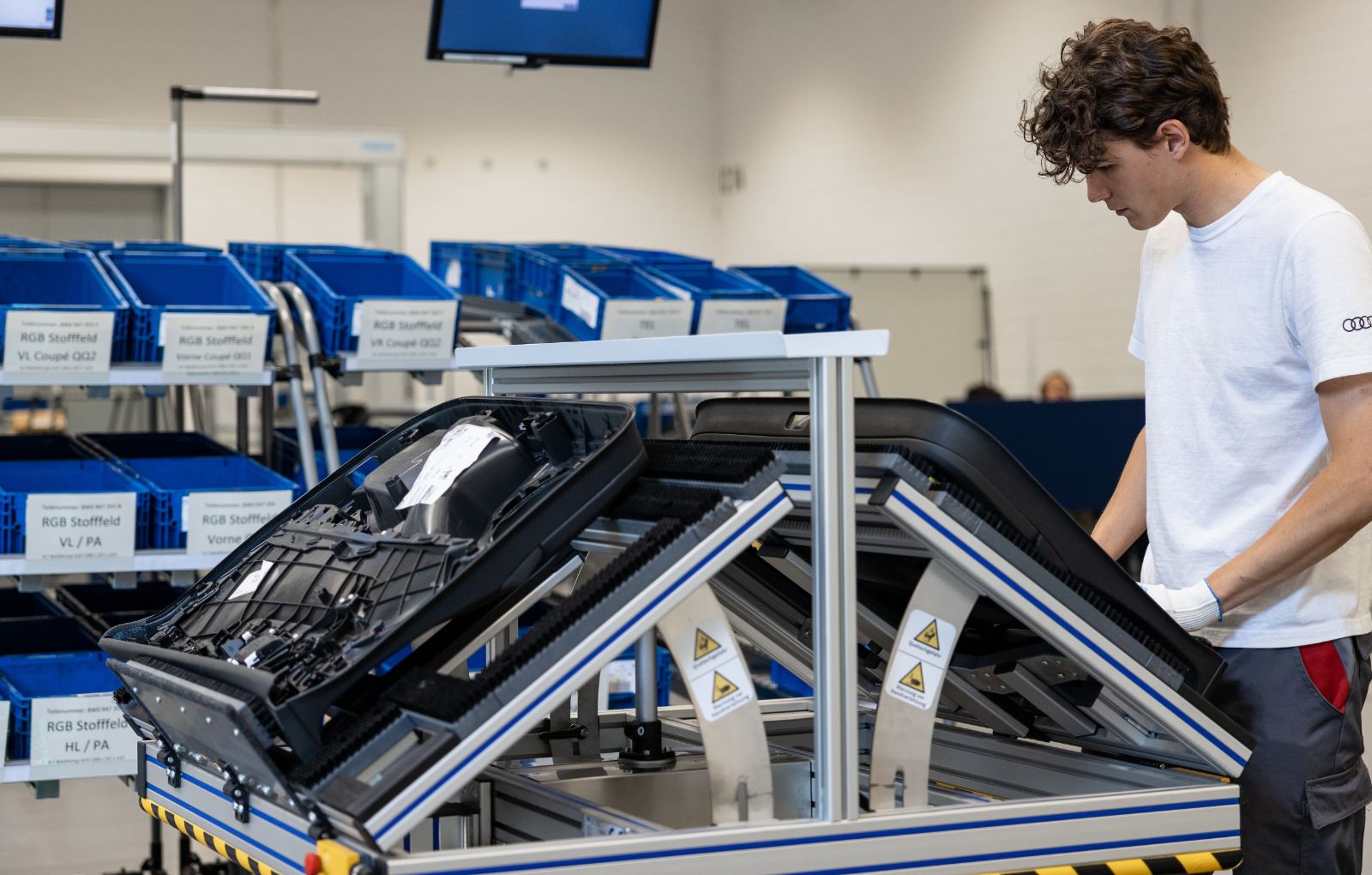
În acest fel, asamblarea este mai rapidă, iar productivitatea a crescut cu 20% în unele cazuri, având în vedere că munca angajatului este mult ușurată. De fapt, acesta este unul dintre avantajele majore ale asamblării modulare.
Mai puțină presiune pe angajat duce la o productivitate crescută. Destul de simplu. Nu?
REALITATEA VIRTUALĂ, COMPONENTĂ CHEIE ÎN PRODUCȚIA VIITORULUI
O altă modalitate prin care Audi intenționează să eficientizeze procesul de producție este, deloc surprinzător, realitatea virtuală. Acest mediu tridimensional, generat de computer, elimină toate limitele palpabile și permite, spre exemplu, ca un design să ajungă mai rapid în producția de serie și, mai apoi, la client.
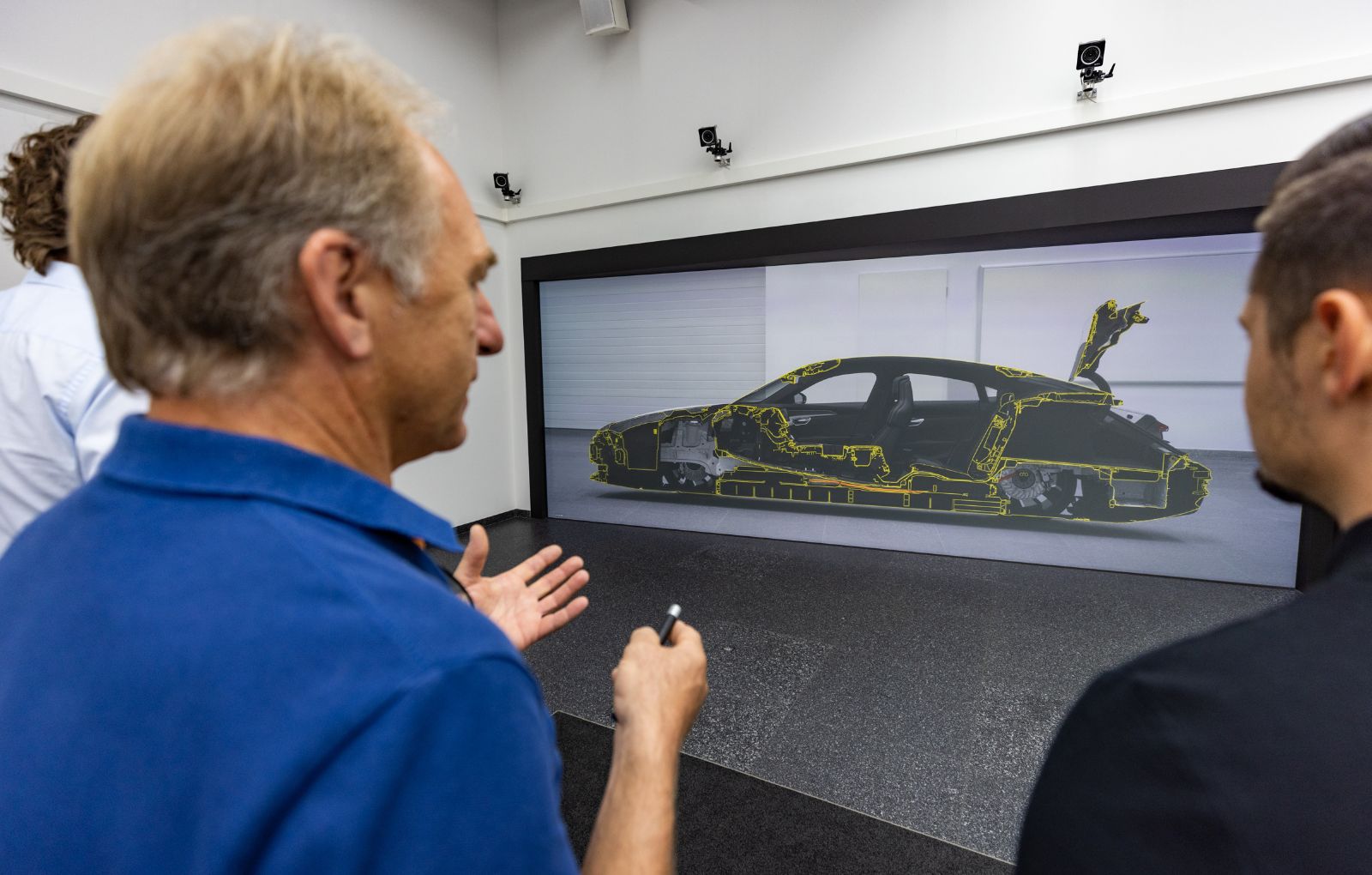
Constructorul din Ingolstadt utilizează niște ecrane uriașe pe care mașinile pot fi vizualizate în mărime naturală. Și nu doar atât. Ele pot fi iluminate dinamic, cu umbre și reflexii, pentru ca inginerii să interacționeze cu ele din perspectiva clientului.
Tot cu ajutorul acestei tehnologii, Audi se asigură că poate dezvolta o anumită piesă, atât din punct de vedere constructiv, cât și calitativ. Efectele instalării unei componente noi și toleranțele de asamblare pot fi apoi văzute în imaginea de ansamblu a mașinii.
În acest fel, inginerii din cadrul diviziei de producție pot modifica oricând designul, fără costuri adiționale prea mari, chiar din unitățile de producție.
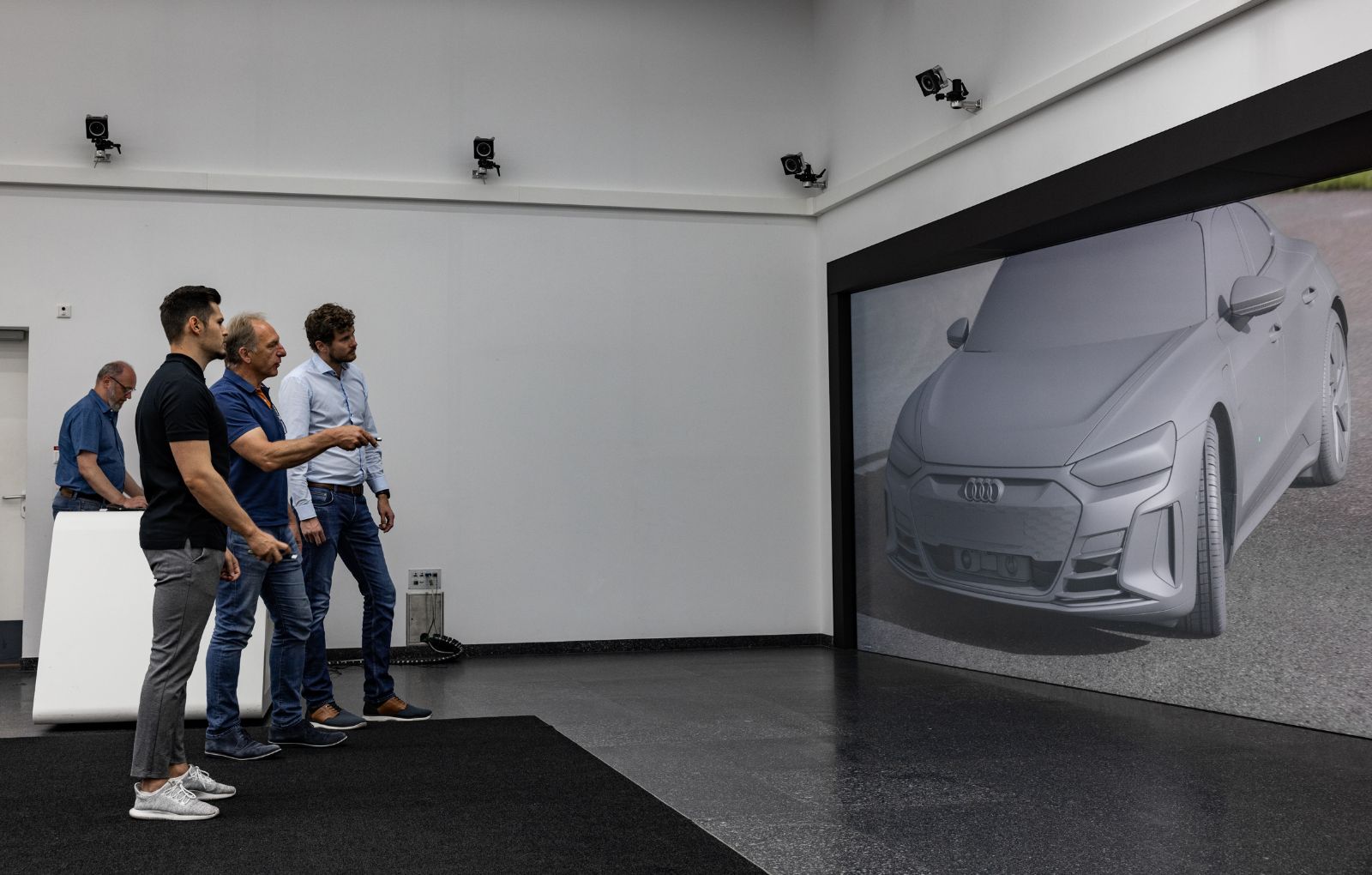
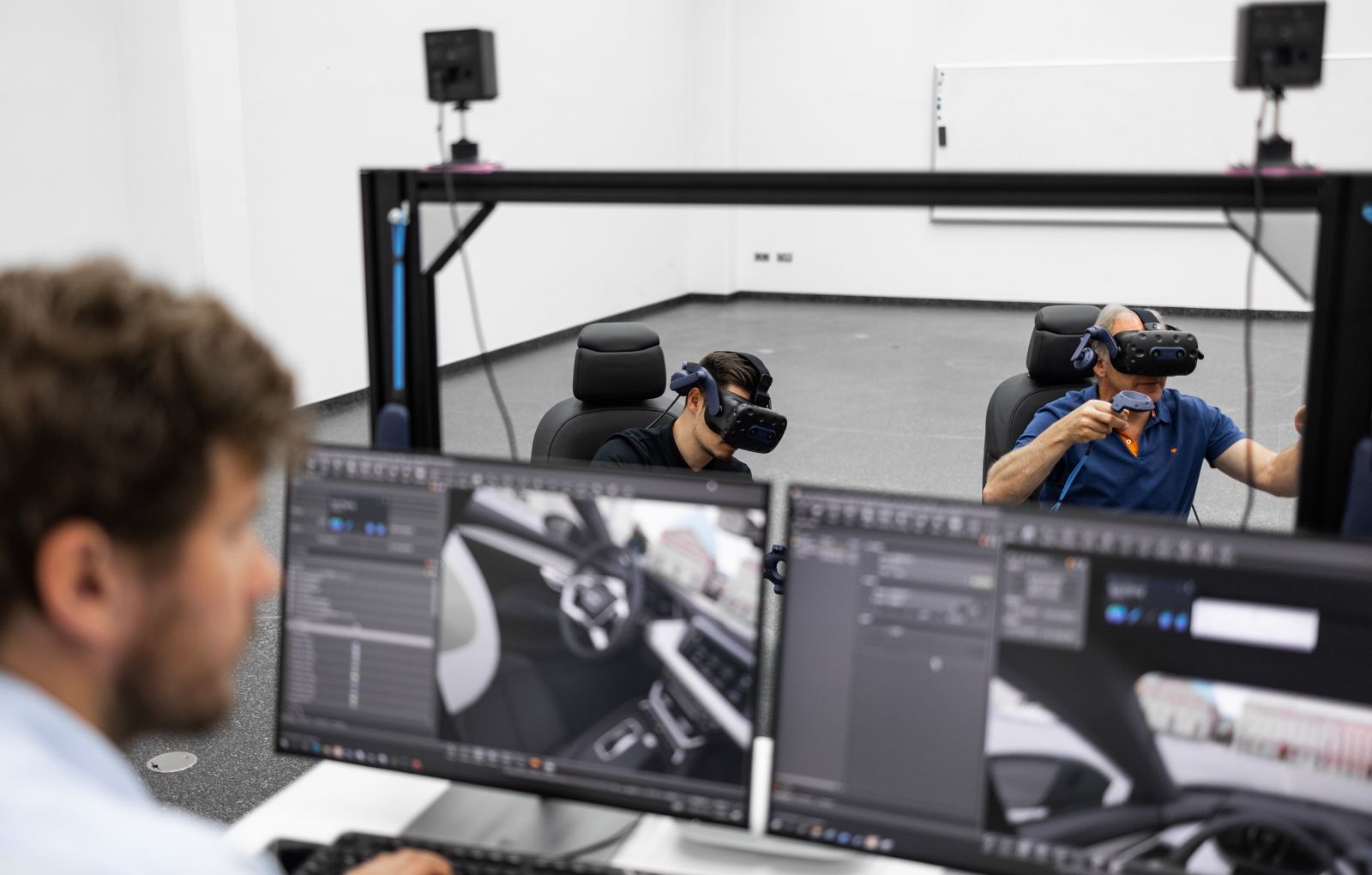
SPOT: CÂINELE ROBOT PENTRU SCANĂRI 3D
Risipa de materiale este un factor important pentru a obține o producție inteligentă și sustenabilă. Pentru a stopa acest fenomen, Audi a apelat la planificarea virtuală a asamblării componentelor. Acest lucru elimină construirea de prototipuri în procesul de planificare.
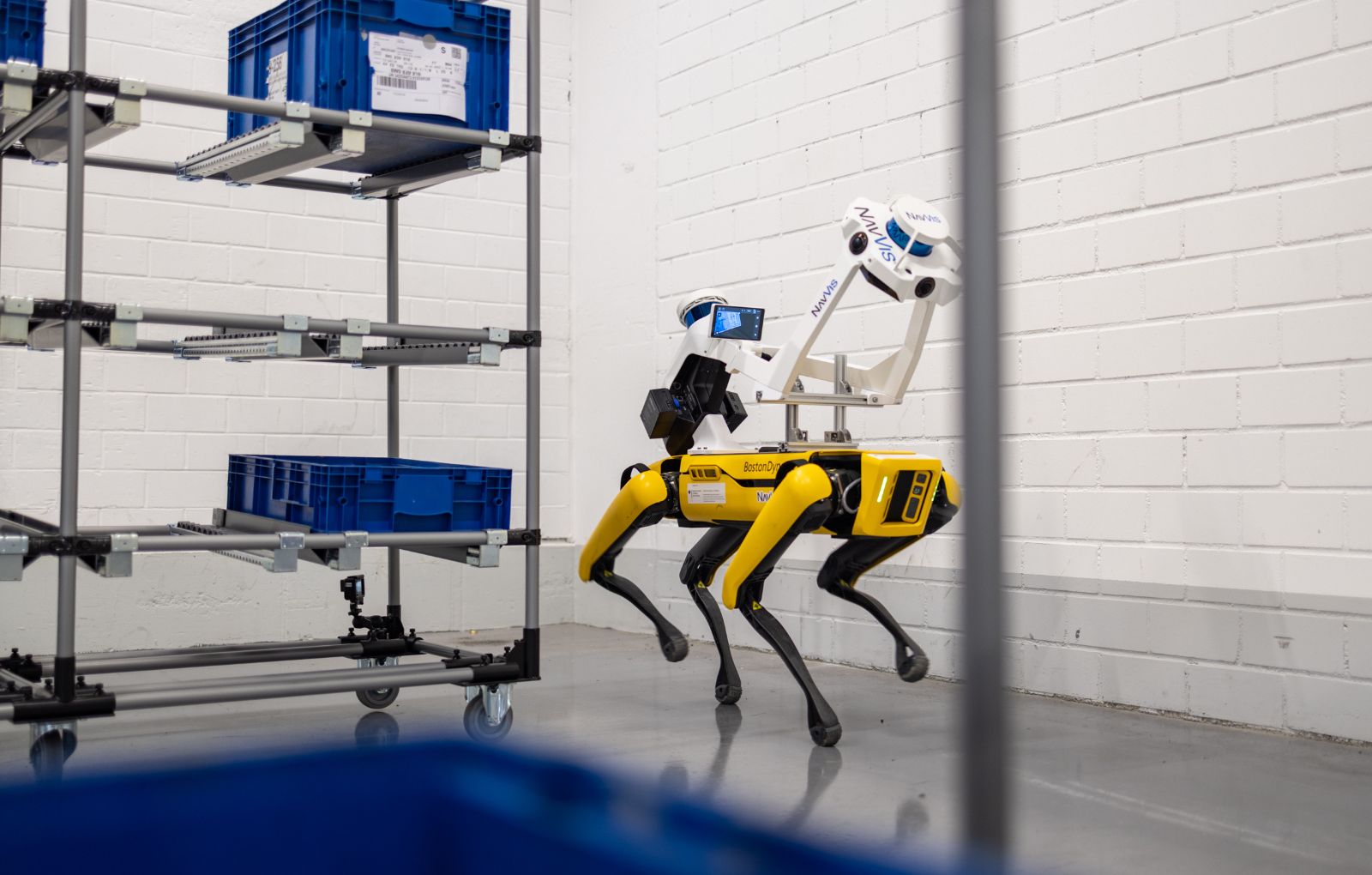
Cu ajutorul unui software bazat pe inteligența artificială, angajații mărcii din Ingolstadt pot naviga virtual prin liniile de asamblare. În acest fel, pot compara diverse locații și utilizează soluții adecvate din alte linii de producție în planificarea lor.
În ultimii 5 ani, de când a început acest proces de digitalizare, Audi a scanat 3D aproximativ 4 milioane de metri pătrați din 13 uzine. Ca să îți faci o idee, scanarea a 100.000 de metri pătrați durează circa 3 săptămâni, având în vedere că poate fi realizată doar noaptea sau în weekend.
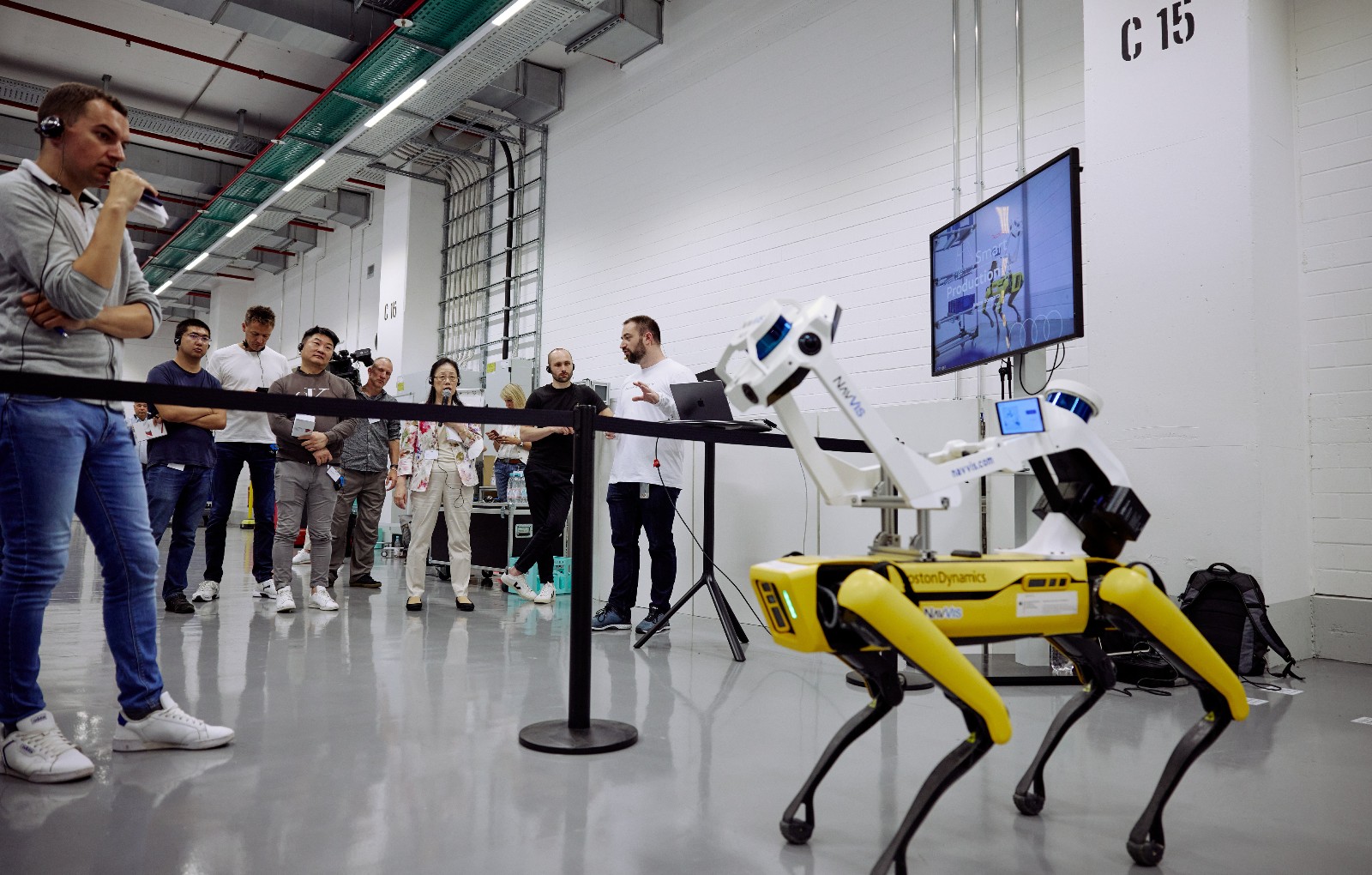
Pentru a grăbi procesul, Audi testează, din decembrie 2021, un câine robot, denumit Spot. Acesta scanează aceeași suprafață în doar 48 de ore, iar ruta și-o calculează în mod autonom. Rezultatele sunt, potrivit reprezentanților companiei, extrem de promițătoare.
REȚEA „NEURALĂ” ARTIFICIALĂ
Inteligența artificială este utilizată și în alte părți ale procesului de producție. Un algoritm bazat pe inteligență artificială identifică piesele cu defecte de fabricație la uzina din Ingolstadt: o dată identificate, aceste defecte sunt mai apoi evidențiate în mod corespunzător.
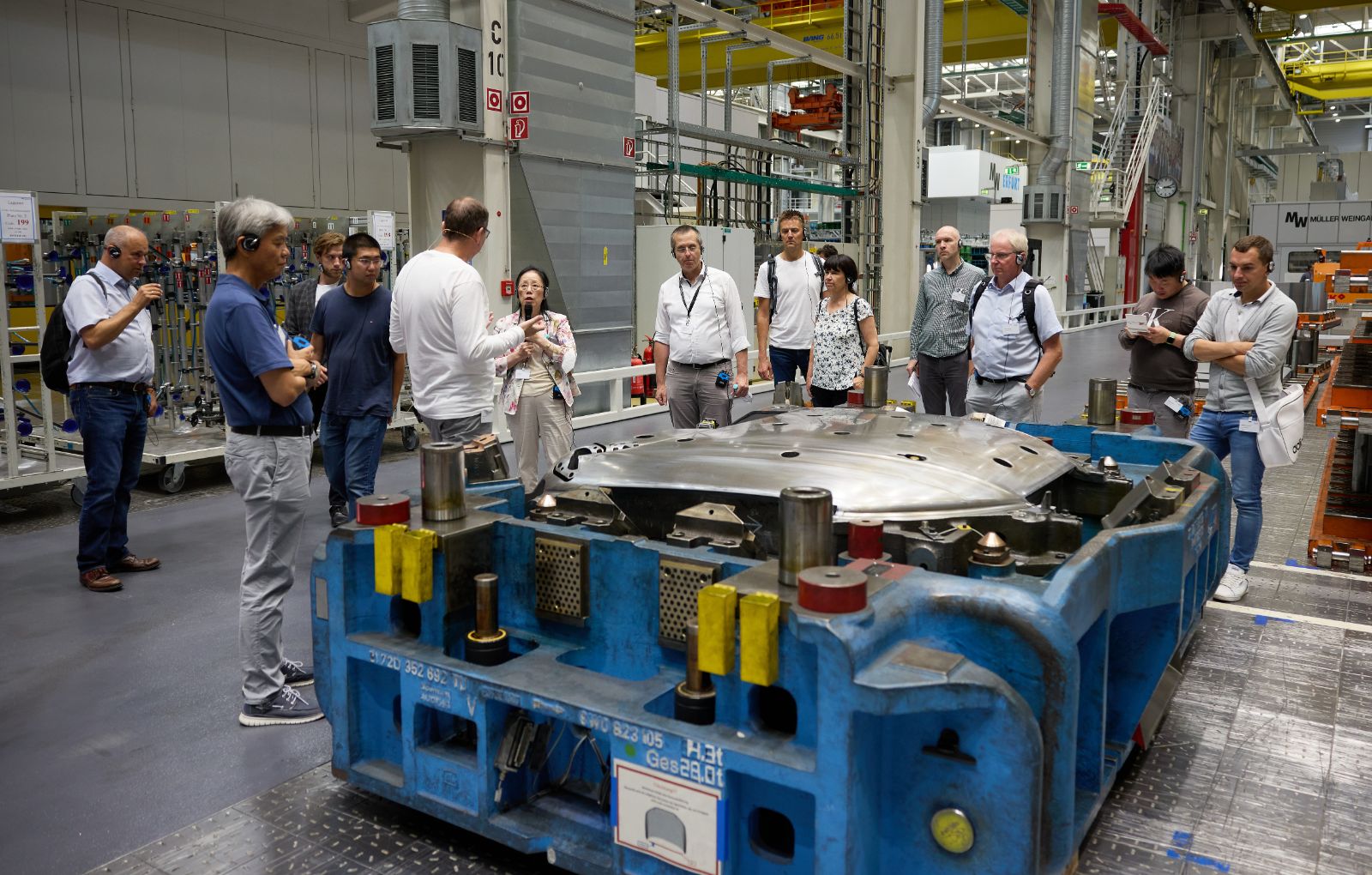
Această rețea neurală artificială a învățat să recunoască defectele de fabricație după ce a analizat câteva milioane de șabloane și terabiți de imagini de la mai multe uzine Audi și Volkswagen.
Tot cu ajutorul inteligenței artificiale este testată și calitatea punctelor de sudură, în timp real. Spre exemplu, modelul A6 are circa 5.600 de puncte de sudură care unesc elementele de caroserie și, până acum, calitatea acestora era monitorizată aleatoriu prin realizarea de analize cu ultrasunete.
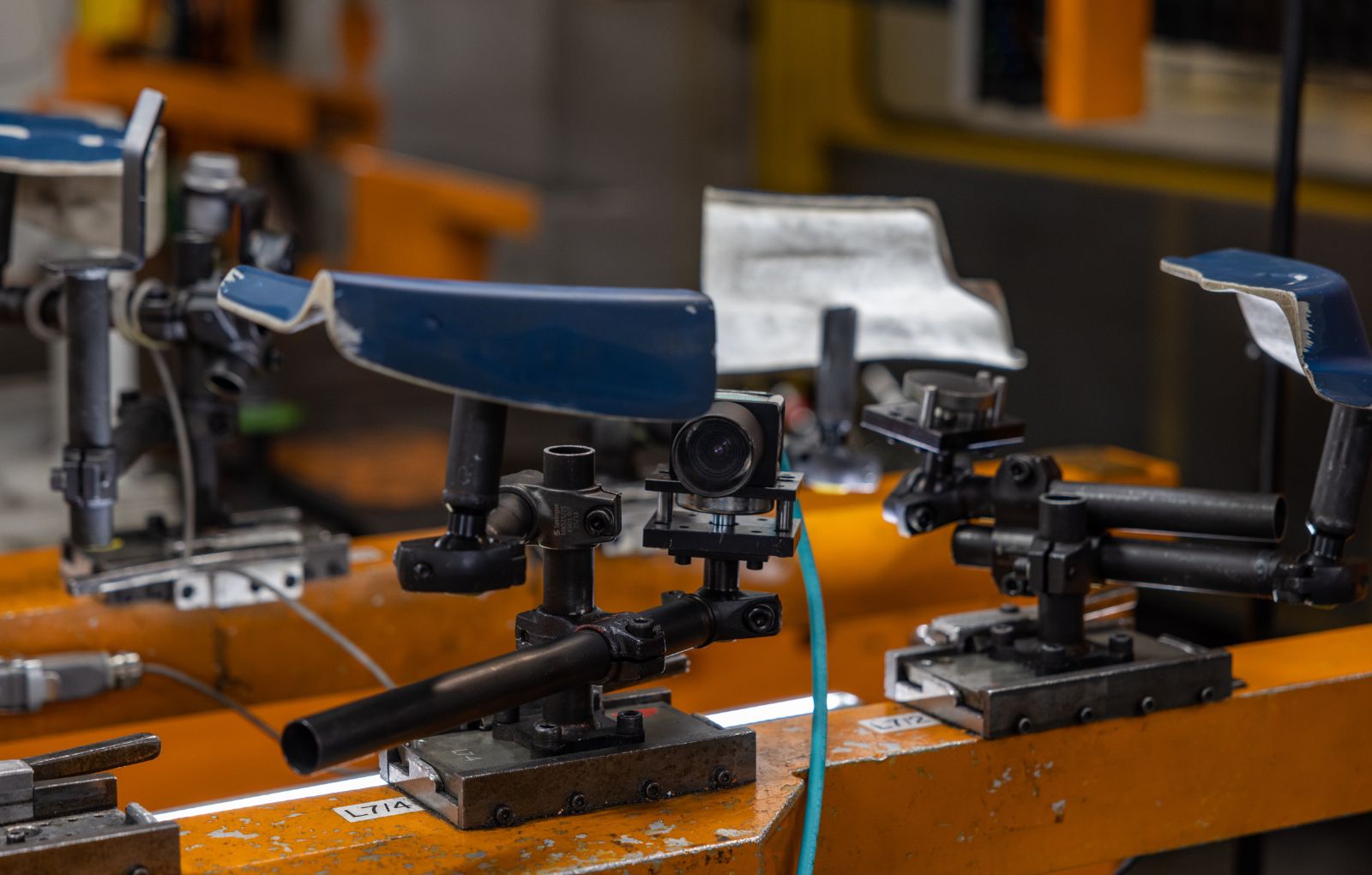
PRODUCȚIE BAZATĂ PE STOCARE ÎN ETER
Suntem în era tehnologizării. Un moment numai bun pentru ca Audi să treacă de la o producție bazată pe hardware, la una bazată pe software. Mai exact, constructorul din Ingolstadt vrea să folosească servere locale, în locul calculatoarelor industriale.

Soluția propusă de germani este numită Edge Cloud 4 Production și reprezintă o schimbare de paradigmă în tehnologia automatizării.
După ce au fost testate în Laboratorul de Producție, trei servere locale se regăsesc acum la uzina Bollinger Hofe, acolo unde se produc modele ca e-tron GT quattro și R8. Pentru că produce un număr relativ mic de mașini, această fabrică este utilizată ca o platformă de testare pentru soluțiile inovatoare Audi.
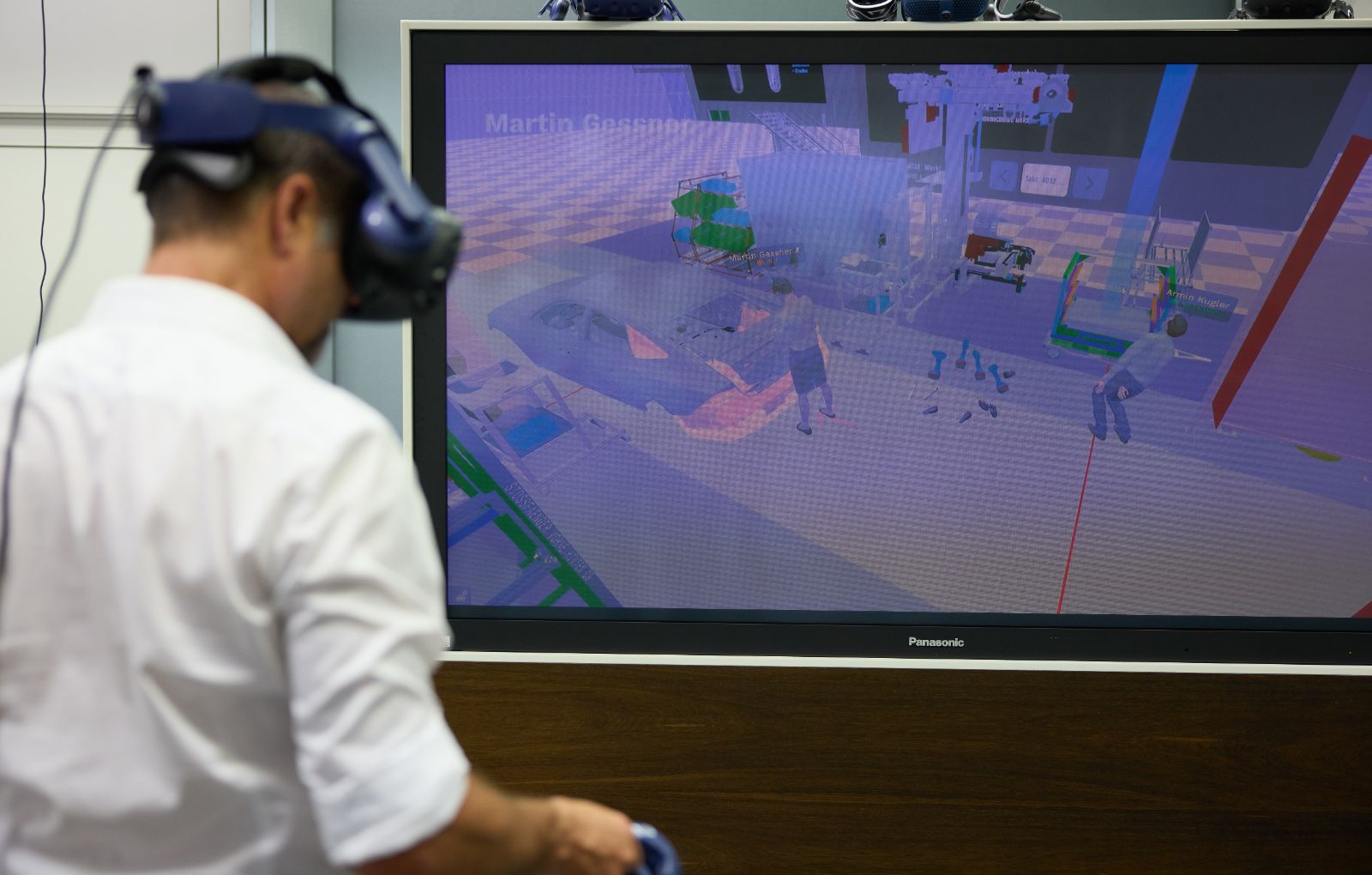
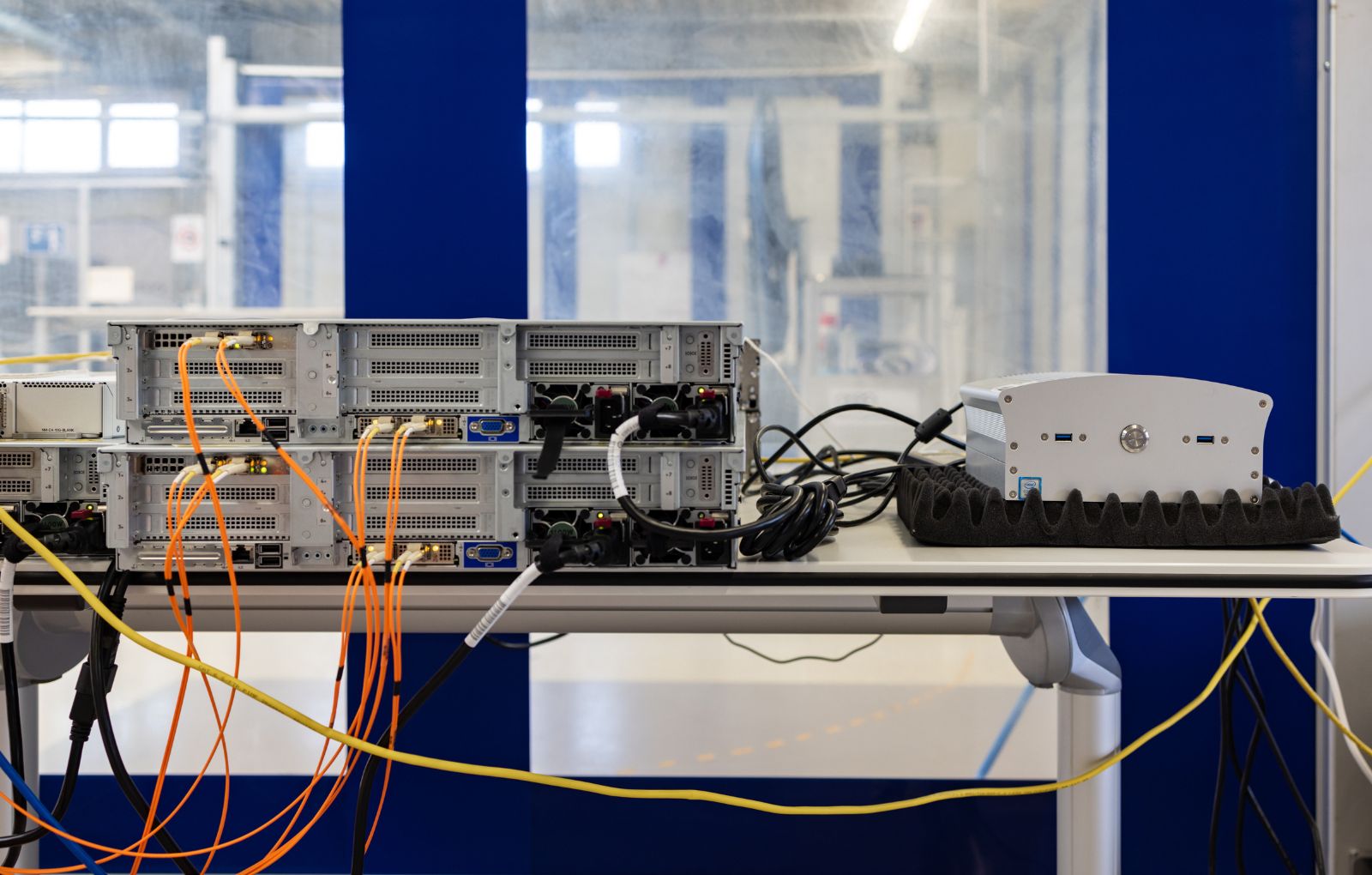
„Obișnuiam să achiziționăm soluții hardware când voiam să lansăm noi funcții. Cu acest Edge Cloud 4 Production, cumpărăm aplicații sub formă de software. Acesta este un pas crucial către o producție bazată pe IT,” este de părere același Gerd Walker.
Dacă acest tip de infrastructură se dovedește fiabilă, ea va fi implementată la nivel de grup.
CONSERVAREA ENERGIEI, VITALĂ PENTRU O PRODUCȚIE SUSTENABILĂ
Cantitatea de energie pe care o consumă uzina Audi din Ingolstadt într-un an este echivalentă cu cea pe care o consumă întregul oraș, în aceeași perioadă de timp.
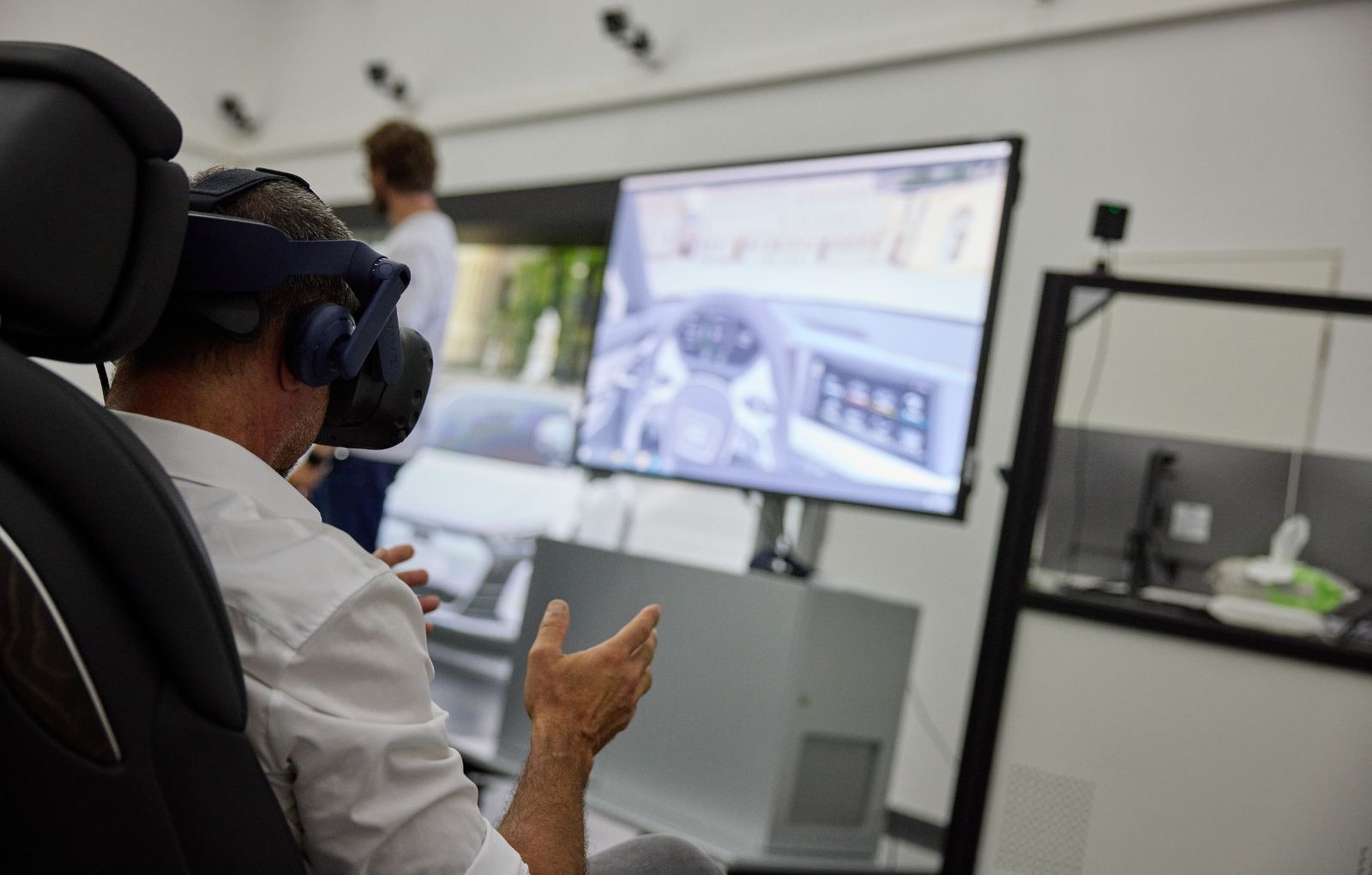
Pentru a avea o producție sustenabilă, constructorul german a trebuit să învețe cum să conserve această energie. A făcut-o cu ajutorul unui „instrument” software, dezvoltat in-house. Numele său este Energy Analytics și a permis evidențierea consumurilor mari de energie, în perioadele de producție și atunci când producția este oprită.
Prin analizarea mai multor consumatori mari (inclusiv aparatele de sudură, cabinele de vopsit, sistemele de iluminat și de ventilație), Audi poate monitoriza consumul de energie. În cazul unei depășiri, se poate găsi cauza și mai apoi se pot lua decizii pentru a scădea consumul de energie.
În 2021, prin utilizarea Energy Analytics, Audi a salvat circa 37.000 MWh la uzina din Ingolstadt.